Überwindung von Herausforderungen in der metallischen additiven Fertigung
Die metallische additive Fertigung, auch bekannt als Metall-3D-Druck hat die Art und Weise, wie wir Metallteile herstellen, revolutioniert. Dennoch gibt es einige Herausforderungen, die bei diesem innovativen Prozess auftreten können. In diesem Blogbeitrag werden wir die häufigsten Herausforderungen bei der metallischen additiven Fertigung besprechen, darunter Rissbildung, Verzug und Oberflächenrauheit. Wir werden auch Methoden untersuchen, wie diese Schwierigkeiten überwunden werden können, anhand eines praxisnahen Beispiels. Starten wir mit der ersten Herausforderung…
Herausforderung 1: Rissbildung:
Rissbildung ist eine der häufigsten Herausforderungen in der Metall-additiven Fertigung, zumindest wenn das Material nicht optimal ausgewählt ist. Die Materialabhängigkeit sorgt in Sachen Rissbildung für große Unterschiede beim Ergebnis. Während des Abkühlungsprozesses können interne Spannungen auftreten, die zu Rissen im gedruckten Teil führen können. Diese beeinträchtigen die mechanischen Eigenschaften und die Zuverlässigkeit des Teils.
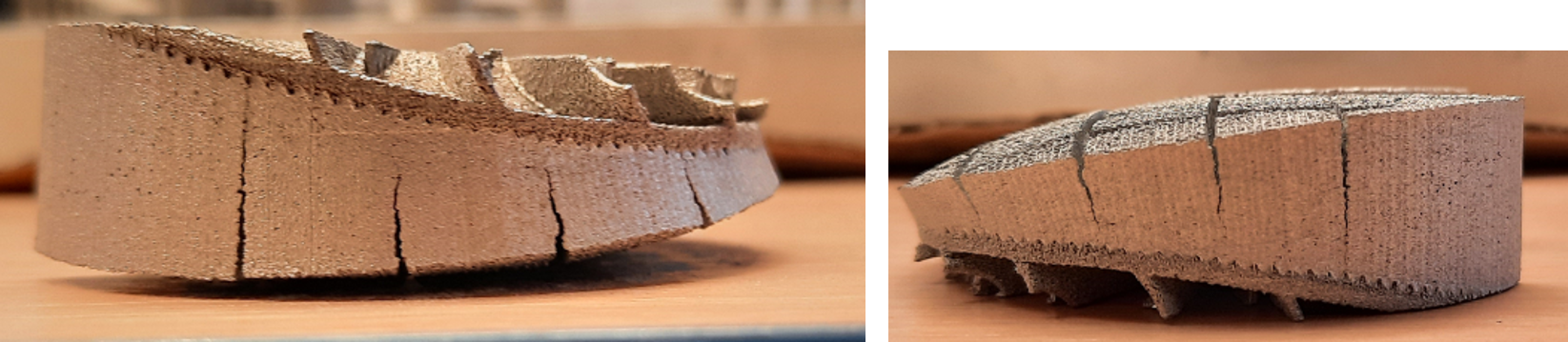
Lösung: Die Kontrolle der Prozessparameter wie Scangeschwindigkeit, Vorwärmung und Schichtdicke ist entscheidend, um Rissbildung zu minimieren. Post-Processing-Methoden wie Wärmebehandlung können ebenfalls angewendet werden, um interne Spannungen abzubauen. So händeln sie die Herausforderung Rissbildung!
Herausforderung 2: Verzug:
Verzug ist ein weiteres häufiges Problem. Während des Abkühlungsprozesses können sich Teile verziehen oder verformen, was zu Abweichungen von den gewünschten Abmessungen führen kann.
Lösung: Aber wie geht man mit dieser Herausforderung um? Die Optimierung der Prozessparameter, insbesondere der Wärmeableitung, kann Verzug reduzieren. Die Verwendung von Stützstrukturen, die während des Druckens unterstützen und nachher entfernt werden, kann ebenfalls dazu beitragen, Verzug zu minimieren.
Herausforderung 3: Oberflächenrauheit:
Die Oberflächenrauheit ist ein wichtiges Qualitätsmerkmal für metallische 3D-gedruckte Teile. Unbehandelt können diese Teile eine raue Oberfläche aufweisen, die möglicherweise nicht den Anforderungen entspricht.
Lösung: Eine nachträgliche Oberflächenbearbeitung, wie Schleifen oder Polieren (Strahlen), kann die Oberflächenrauheit verbessern. Die Anpassung der Druckparameter und der Einsatz von geeignetem Druckumfeld können ebenfalls zu glatteren Oberflächen führen.
Praxisbeispiel: Überwindung von Rissbildung in der Luftfahrtindustrie:
Die Luftfahrtindustrie nutzt die metallische additive Fertigung für die Herstellung von Triebwerksteilen. Ein konkretes Beispiel ist das Auftreten von Rissen in 3D-gedruckten Turbinenschaufeln aufgrund von interner Spannung während des Abkühlungsprozesses. Um dieses Problem zu bewältigen, haben Ingenieure die Prozessparameter genau analysiert und optimiert. Durch die Anpassung der Scangeschwindigkeit und der Wärmeableitung konnten sie die Rissbildung minimieren und hochwertige Turbinenschaufeln herstellen.
Fazit:
Die metallische additive Fertigung bietet unbestreitbare Vorteile, geht jedoch mit einigen technischen Herausforderungen einher. Wichtig ist natürlich auch die Auswahl des richtigen Metallpulvers, um Probleme im weiteren Prozess zu verhindern. Rissbildung, Verzug und Oberflächenrauheit sind nur einige der Schwierigkeiten, die überwunden werden müssen. Durch eine Kombination aus Prozessoptimierung, Materialentwicklung und Post-Processing-Methoden können diese Herausforderungen erfolgreich bewältigt werden. Die Praxis zeigt, dass die Überwindung dieser Schwierigkeiten zu hochwertigen, zuverlässigen und leistungsfähigen 3D-gedruckten Metallteilen führen kann, die eine breite Palette von Anwendungen bedienen können.